Our visually-pleasing aluminum bridge kits use off-the-shelf components, arriving at your worksite for installation at unparalleled speeds.
Award-winning innovation
- Patented weld-free MakeABridge® system assembles in less than a day with just 3 people and standard tools
- Ideal for new constructions or retrofits of existing structures, for temporary or permanent applications
- Lighter and easier to install than steel
- Recipient of numerous awards for innovation and design, including the Extrusion Technology Foundation’s Design Competition Award
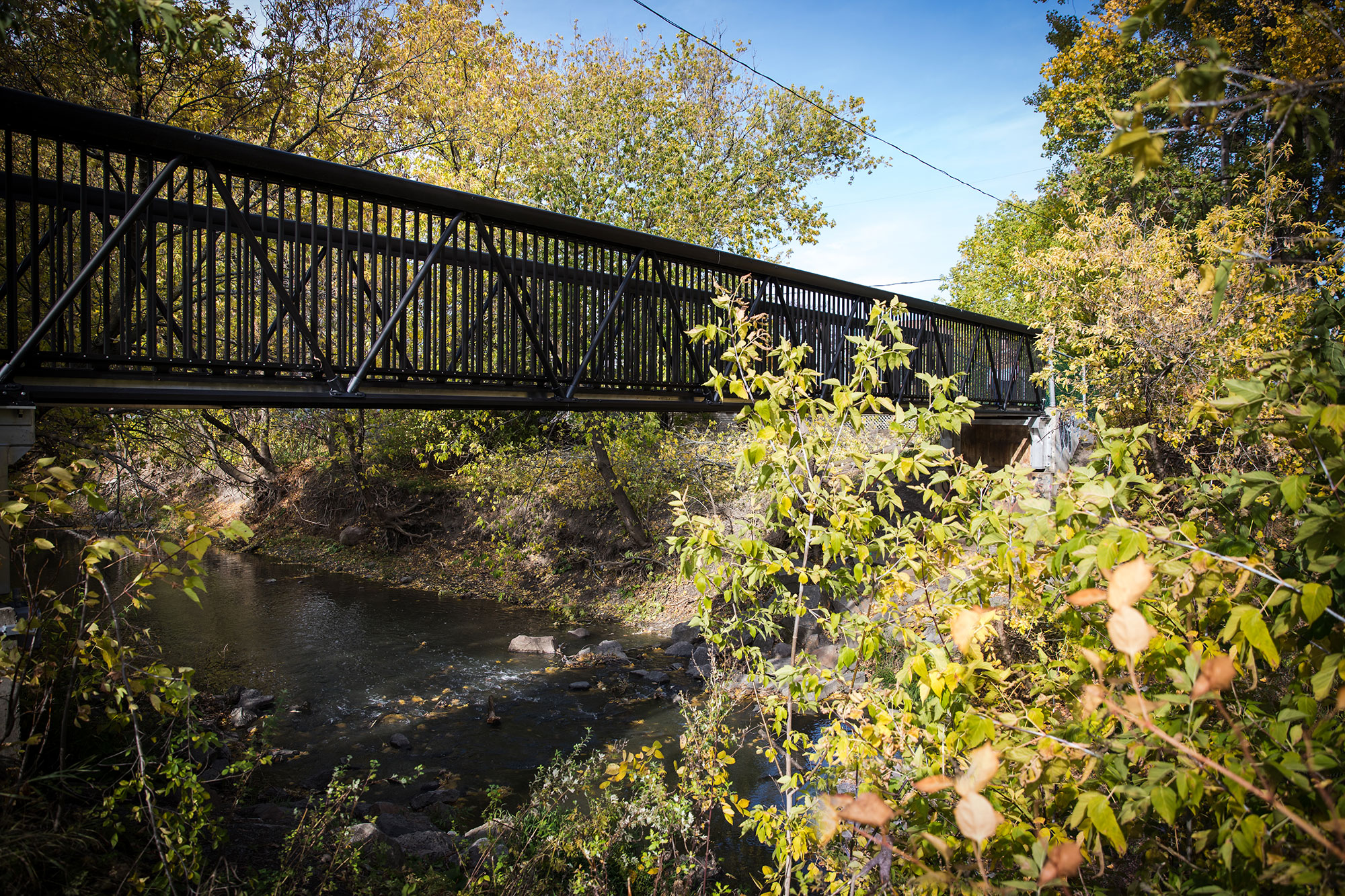
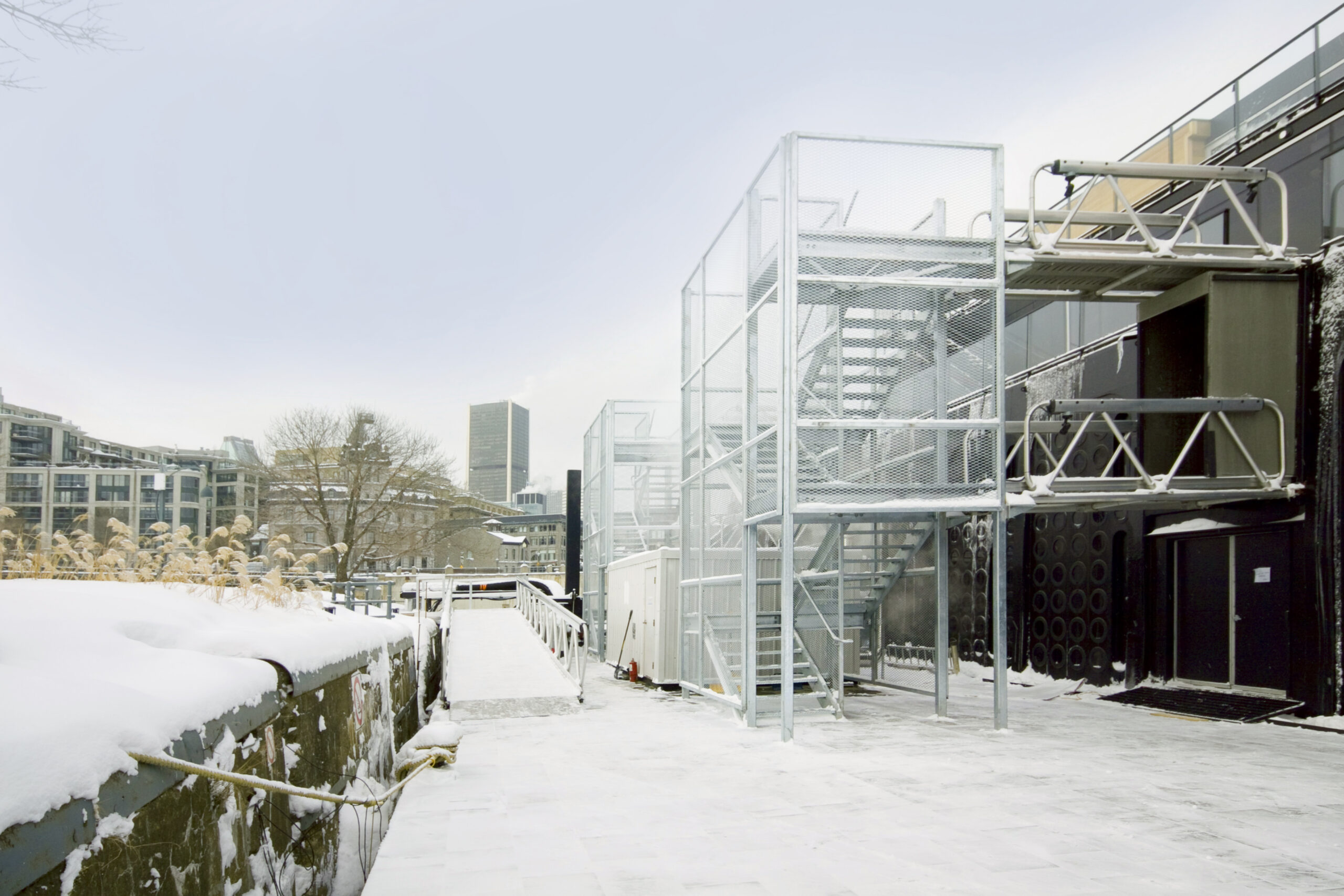
Cost-effective investment
- Easy shipping, with much lower shipping costs than conventional structures
- Includes complete engineering services, eliminating all of the costly phases of design, customized production and approval generally required by a third party
- Resistant to corrosion and extreme weather
- Built with high-strength aluminum to last decades with no maintenance required
Eye appeal
- Refined feel with high-quality materials and careful attention to details
- Standard bridge kit includes clear anodized finish
- Easy to add architectural finish such as anodization and powder coating in a variety of colors
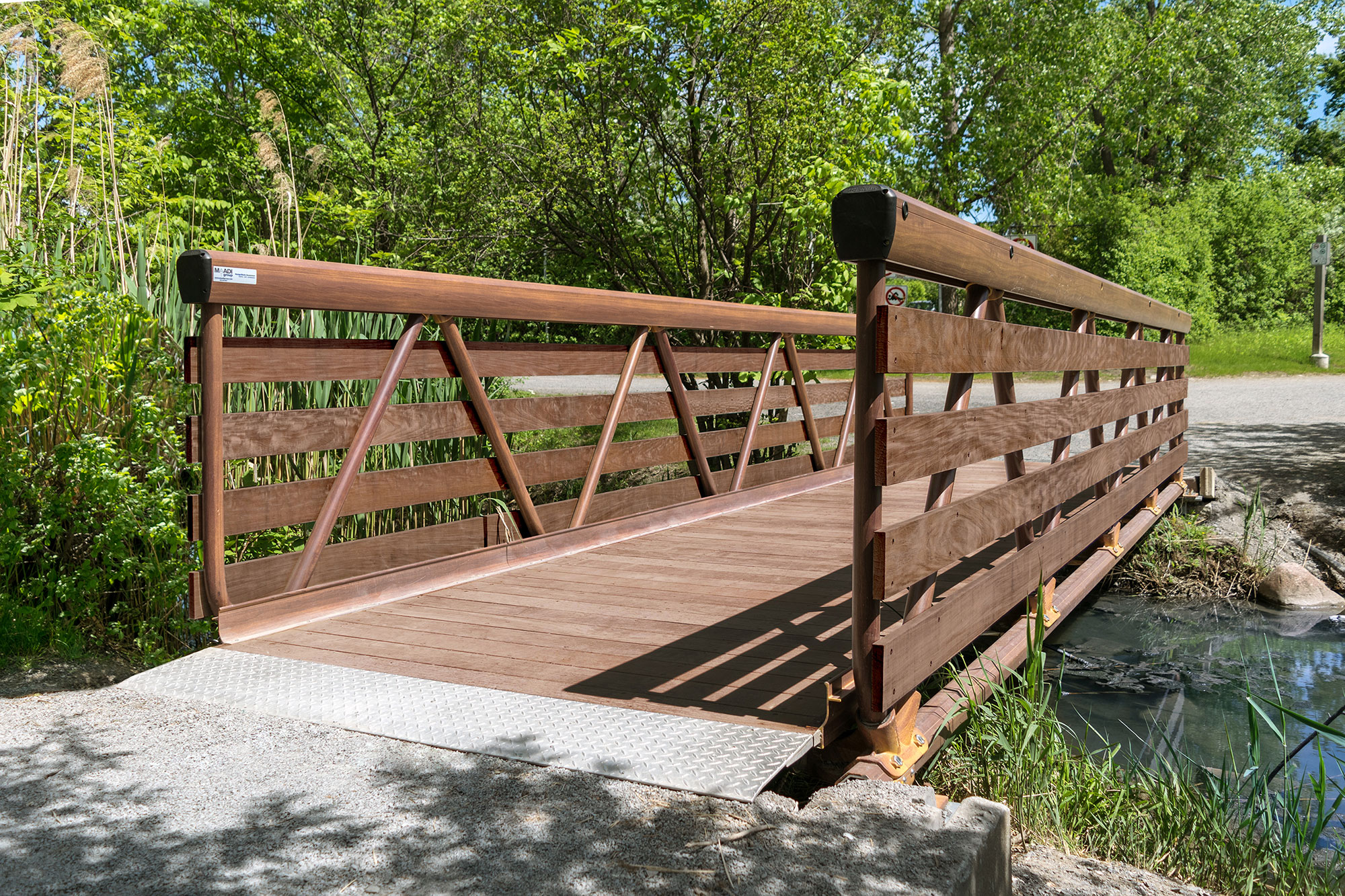
Customized features
Our MakeABridge® aluminum bridge kits offer a wide range of options and are precision-made to your specifications by our top-grade professional engineers.
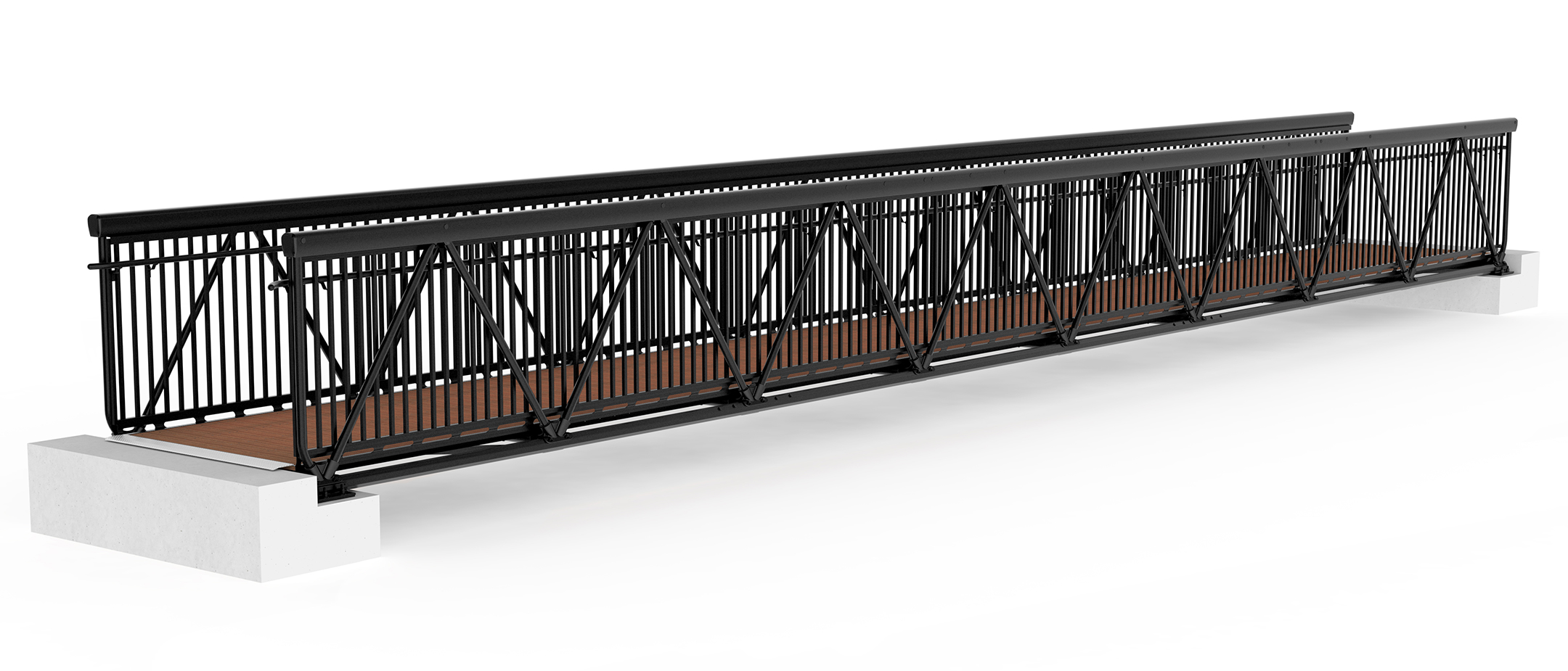
Expertise you can count on for bridge kits
Speedy turnaround
We manufacture our aluminum bridges right in our Canadian plant, eliminating the need to work with a separate supplier. Plus, our bridge kits use off-the-shelf components ready to be shipped pre-assembled or in bundles, making delivery four to eight times faster than for conventional welded bridges.
Experienced engineers
In addition to the hundreds of structural extruded aluminum projects we’ve designed and built, we also have numerous awards under our belt. This includes the Extrusion Technology Foundation’s Design Competition Award in the structural category, which we won a 3rd time in 2022.
Destructive structural testing
A destructive structural test was conducted at the University of Waterloo in Ontario, Canada, in the Department of Civil and Environmental Engineering Structures Laboratory to determine the maximum load capacity of a MakeABridge® bridge system. Read more about the test and the results.
Built to code
All of our design specifications meet local, regional, and national building codes and professional standards as required. All of our technical designs and calculations for our aluminum marine structures bear the seal of one of our professional engineers.

Guaranteed quality
Backed by 15-year limited warranty on aluminum against material failure, defects, and corrosion
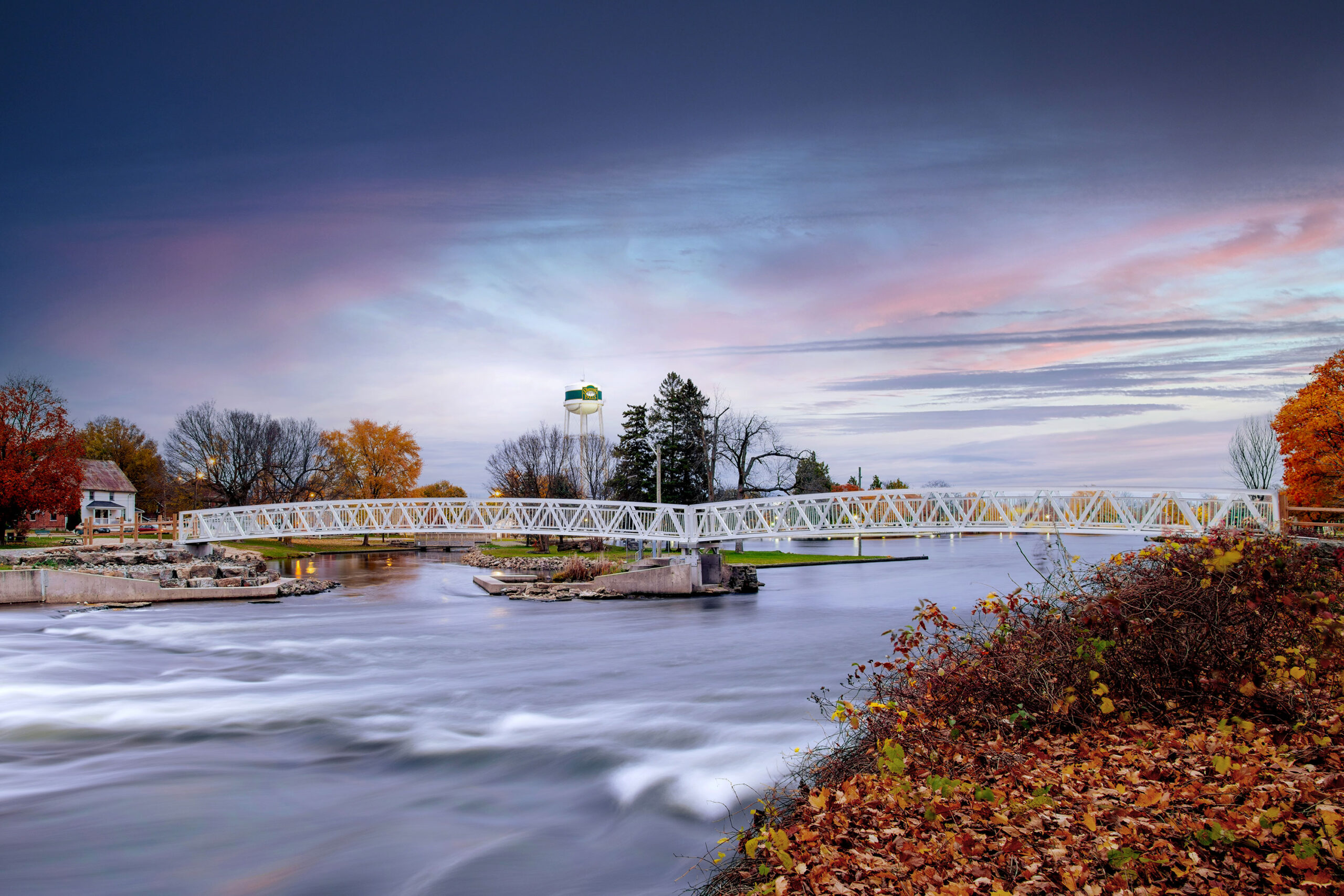
Sector
Civil Structures
We’re your partner for a job well done, no matter how much (or how little) of our expertise you need. Our services include full engineering, technical support and manufacturing, planning, and installation.
Our ServicesDocumentation
Want more details? Download our technical information about our products. And feel free to contact us with any questions!
Other Products
See all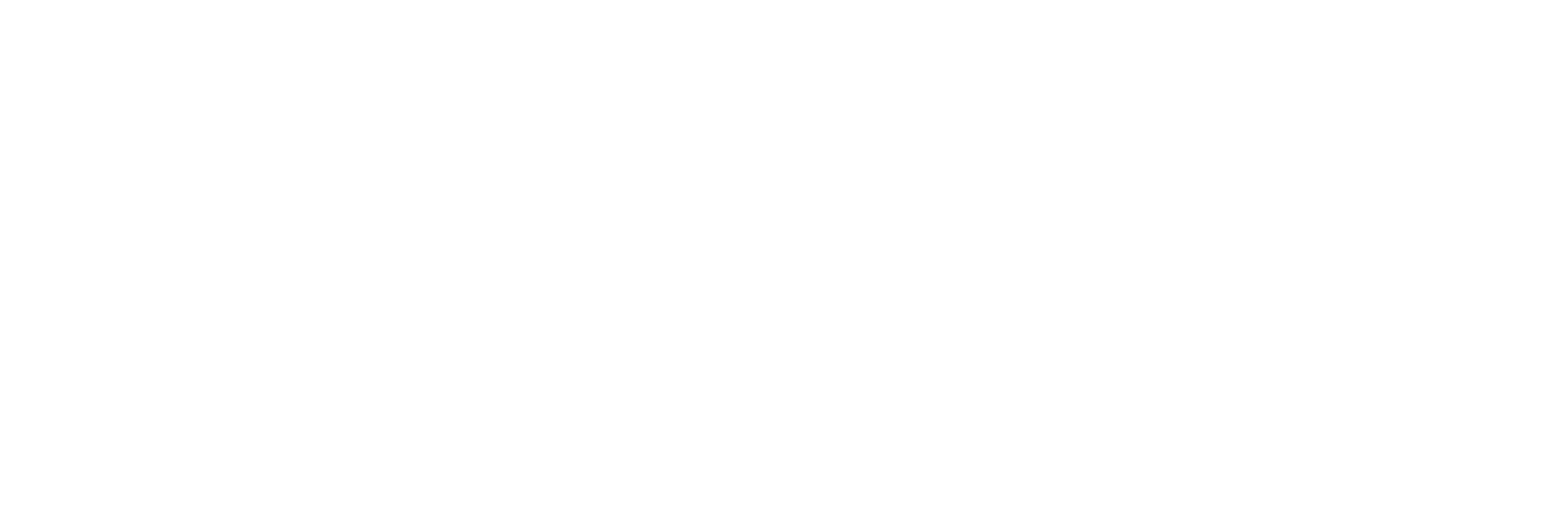
Download your resource
"*" indicates required fields